by NewsAdmin | Jul 20, 2023 | Jendamark Junction
While there has been a lot of hype around Industry 4.0, the digitalisation of factories has not scaled up as expected. A fundamental misconception of what it’s all about and a slow-to-change mindset are two of the major impediments to successful implementation.
A flood of new products on the market and a misplaced focus on the technologies themselves – rather than their practical uses – leaves many customers overwhelmed, says Jendamark innovations director Yanesh Naidoo.
“There are a lot of buzzwords, like the integration of IT and OT on the shop floor, and I think people get befuddled by all the jargon and consulting talk,” Naidoo says.
“Simply put, Industry 4.0 is just a set of technologies that you can use to solve your manufacturing problems.”
A tech toolbox
It helps to think of Industry 4.0 as a toolbox with a set of tools inside, he explains.
“However, having a toolbox full of tools mean nothing unless you do something with them. You must first understand the problem you’re trying to solve in your factory, and then invest in the right tool for the job.
“A hammer has many uses, but how you apply it depends on your situation. Also, you may be trying to hammer in a screw, when what you really need is a screwdriver.”
For example, if frequent machine breakdowns are a problem, Naidoo says an anomaly detector could help to highlight a downward trend in performance, which could be addressed and fixed before it becomes a serious problem, avoiding unnecessary downtime.
Proactive vs reactive approach
“Essentially, Industry 4.0 is about using tools to be more proactive, rather than reactive. But it all means nothing if our mindset doesn’t change.”
Naidoo draws parallels with the preventative approach to health and longevity outlined in Dr Peter Attia’s book Outlived.
“Medicine 2.0 has been extremely successful in treating lifestyle diseases such as Type 2 diabetes. You go to the doctor, they diagnose you and give you insulin, which has saved many lives.
“But this book argues for a transition to a more preventative approach to medicine. Don’t wait to get diabetes; monitor your health, get the check-ups, make the necessary dietary and lifestyle changes, and prevent it from happening in the first place.”
Factory health screening
Until now, manufacturers have not had the technology or toolbox to take a preventative approach to maintaining the overall health of their factory assets, but Industry 4.0 is changing all that. The difference, Naidoo says, lies in the data that comes from continuous measurement rather than a static, point-in-time measurement.
“A factory audit, like a glucose test for diabetes, is not an accurate reflection of your lived reality,” he says.
“For the glucose test, you fast the night before, then go for the blood test. If your results are just within the acceptable range, everything is deemed fine, so you revert to your bad dietary habits. You’ve prepared your body for the test but that’s not how you live your life, and you can expect future problems if you don’t continuously monitor your glucose levels and make lifestyle changes,” explains Naidoo.
Similarly, he says, a factory audit usually runs quality and production checks using the best operators, the best maintenance team, and the best raw materials on the line.
“It’s a fake perception. What you need is live information from the production line that can be used to understand where the problems are and improve the process by making iterative changes.”
The problem with OEE
With the right technology in place, everything on a production line can be measured continuously – from operator speed to press force and scrap rates. The problem, Naidoo believes, is that every plant manager’s performance is measured on Overall Equipment Effectiveness (OEE), which is a widely used, retrospective, reactive measurement.
“It tells you what happened yesterday, but nothing about what is going to happen tomorrow. Plant managers should be measured on what is going to happen, because they can still have an impact on that.”
Like the human body, all production lines are not the same, so trying to meet a set OEE key performance indicator of, say 85%, might not be practical, given the age of the line, or the quality of the incoming raw material.
“The measurement needs to be unique to a particular production line. As the line gets older, there’s more wear and tear, and breakdowns. So, you need dynamic baseline data that reflects the current situation and can be improved year on year.”
Naidoo says technology can help to predict the risks associated with the people, machine, and product parameters on the shop floor. “Then you can proactively do things to mitigate the risk before it happens.
“We know everyone is under pressure to produce. But at some point, when you see the data trends going in the wrong direction, a manager must have the foresight to make the decision to stop the line and fix the problem, knowing it’s eventually going to hit the limit.
“It’s critical to be proactive because when it hits the limit and things break, you will stop the line. And you will have to make the time and budget to fix it. You’ll have far less downtime if you make adjustments when you notice a spike in anomalies, even if they’re still within tolerance.”
Competitive advantage
Ultimately, Naidoo says, Industry 4.0 is a must for manufacturers who want to remain in business in a rapidly changing environment.
“The world is getting far more competitive. You have to squeeze every single cent you can out of your production process. One of the key things is to become more agile because variation of product, or mass customisation, is now a demand from customers. Your production line needs to be able to adapt quickly and effectively, and also manage fluctuating volumes, without massive capital cost or too much downtime.”
So, what does practical digitalisation look like and where does one start?
If a customer is still hesitant to make changes on the production side, Naidoo says one easy entry point is digitising the maintenance function to facilitate the scheduling of tasks and a more preventative approach to asset health.
“Then once you start seeing the benefits, you can start optimising your assembly process efficiencies by introducing, for example, operator guidance systems. If you choose the right supplier and technology, digitalisation is designed to start small and grow with you step by step, so you get your return on investment.”
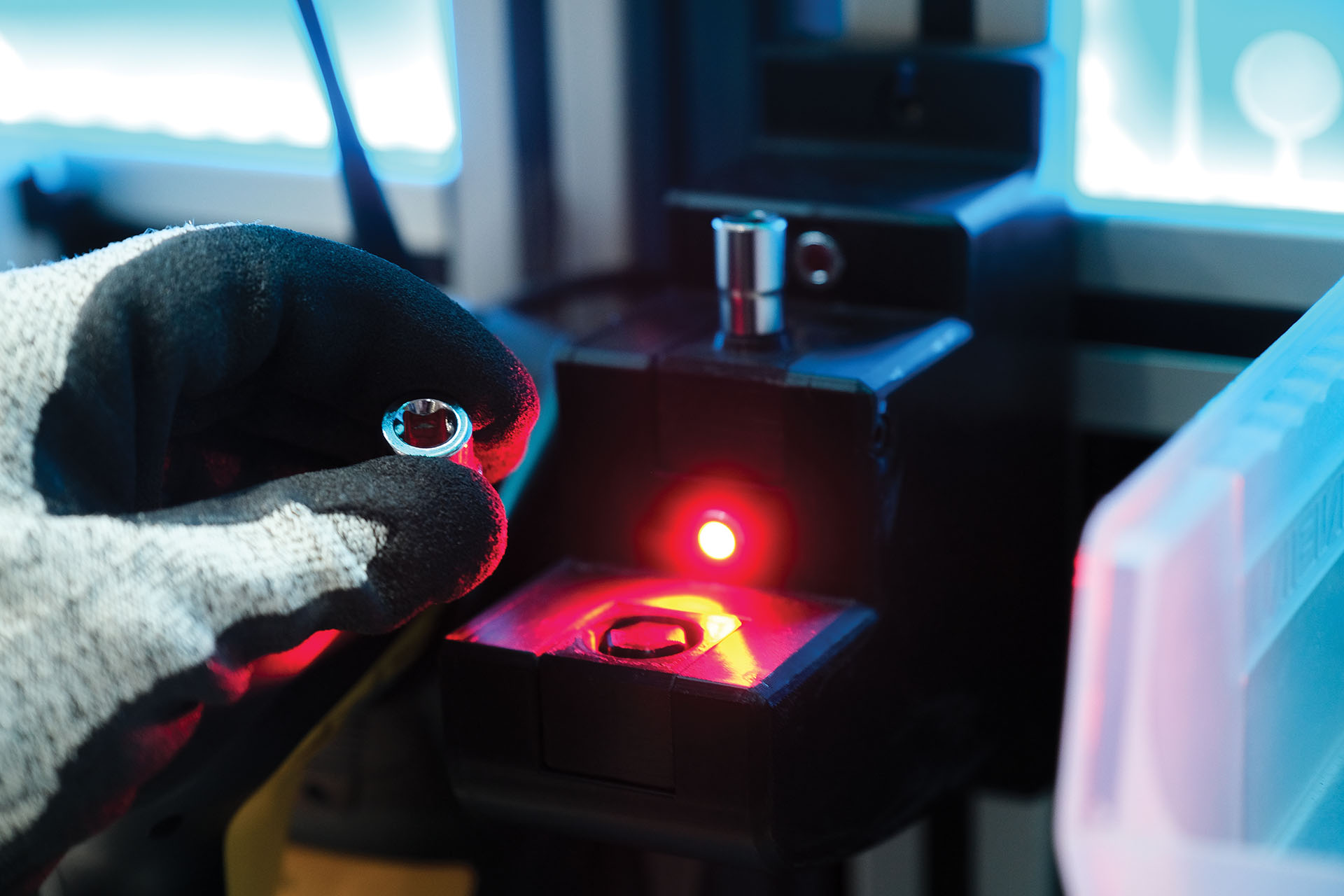
by NewsAdmin | Apr 4, 2023 | Jendamark News
Jendamark Automation is proud to have been named Technology Company of the Year at the Africa Tech Week awards in Cape Town in September.
The company was recognised for its technological achievements in developing digitally enhanced component assembly systems for the global automotive sector, which contributed to its commercial success, while showcasing opportunities for economic transformation in Africa.
Founder and managing director Quinton Uren says he is delighted that Jendamark’s digital transformation journey has been recognised and rewarded.
“I am incredibly proud of our young and dynamic team who have led the way. Over the past few years, Jendamark has shifted rapidly from a historically automation-focused company in the manufacturing space into a diversified global tech leader.
“What remains unchanged, however, is our focus on understanding and meeting our customers’ needs.”
Digital ubuntu
Jendamark’s innovations director, Yanesh Naidoo, says the company’s digital manufacturing technologies deliver an African-born, human-centric response to the demands of Industry 4.0.
Unlike more developed economies, where a shrinking workforce necessitates automation, the future of developing economies lies in unlocking their human capital, explains Naidoo.
“Instead of automating processes that take people off production lines, we are developing tech to unleash human potential. We call it ‘digital ubuntu’, and believe it is the only way to bring more people into the economy and empower them to contribute to society,” he says.
“Jendamark’s manufacturing presence in South Africa and India allows us to understand the challenges that many developing economies around the world are facing, and we must change the paradigm on how we use technology to solve these challenges.”
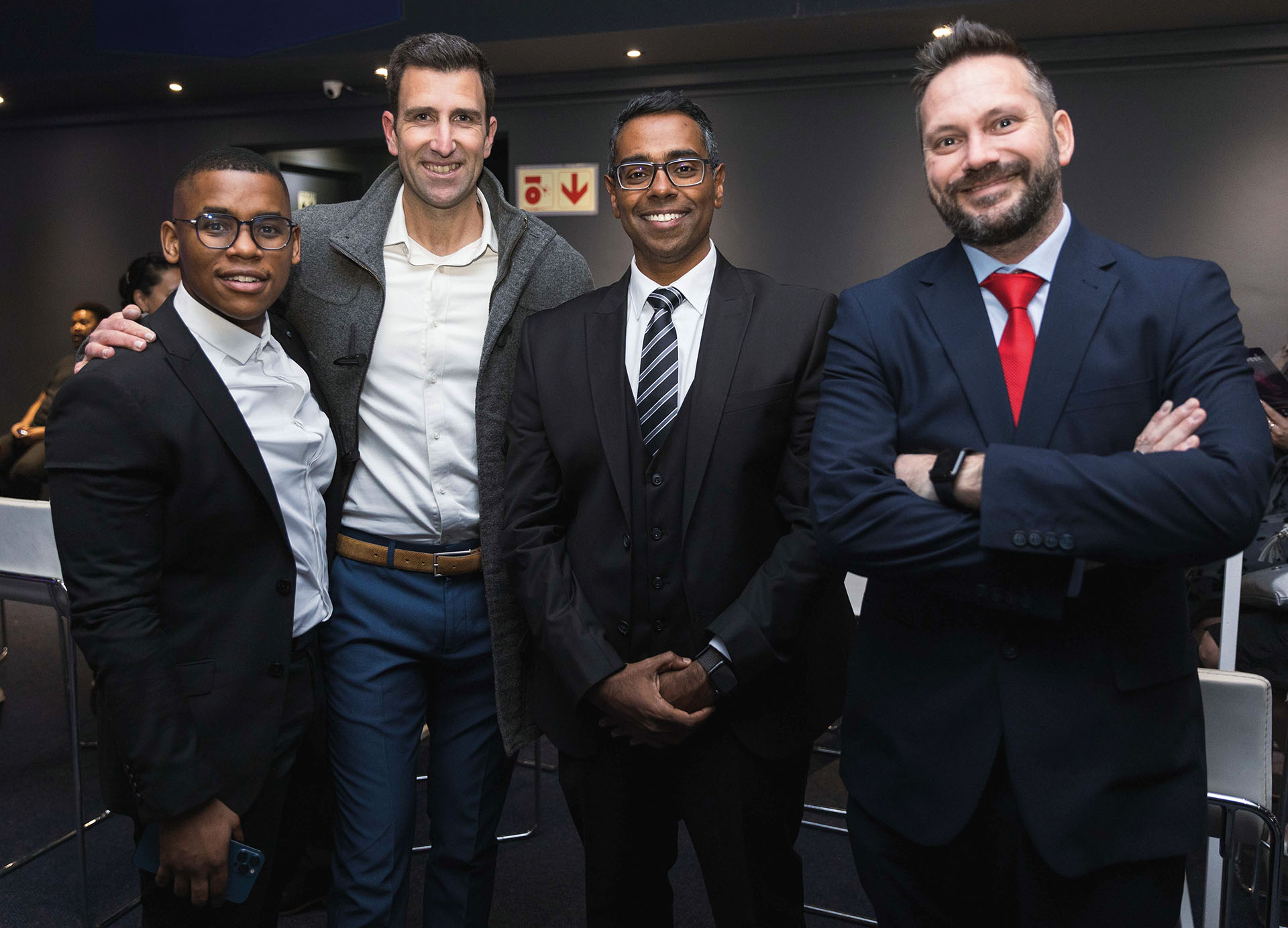
Accelerating digitalisation
Jendamark’s ecosystem of digital productivity and efficiency solutions are marketed under the Odin Manufacturing brand and encompass a range of factory functions from maintenance to quality assurance and real-time reporting on production data.
“We are all incredibly proud of our Odin Manufacturing technologies, but this award is not just for our Odin team,” emphasises Naidoo. “It is for every member of the Jendamark family who works hard to ensure that the facilities we build are world class and ready for the digital revolution.”
Head of Odin Manufacturing Juane Schutte says the win is further validation that Jendamark is solving the right problems.
“We are on a mission to accelerate digitalisation in small and medium factories in Africa at a low cost, allowing semi-skilled shop floor personnel to do much more advanced work. We see human-centric factories as massive opportunities in accelerating skills development and enhancing the economic impact in Africa.”
Scan this QR code to watch the competition entry video showcasing Jendamark’s journey.
by NewsAdmin | Mar 21, 2023 | Jendamark News
While Jendamark applies ecosystem thinking to the development of all our manufacturing technologies, we recently invested in an ecosystem of a different sort in our quest to be the employer of choice.
In October, Jendamark Automation announced an investment in conservation which will transform one of Nelson Mandela Bay’s most controversial game parks into a private sanctuary that aims to restore biodiversity and promote wildlife education.
The company purchased the 120-hectare Seaview Predator Park with the intention to develop it into a conservation and rehabilitation centre that will create jobs and act as an outdoor retreat for Jendamark employees, customers, and community groups.
Wildlife sanctuary
According to operations director Siegfried Lokotsch, Seaview Private Sanctuary, as it is now known, is not a commercial tourism venture and will not be open to the general public.
“However, once we are up and running, any educational or community upliftment programme will be welcome to apply to visit our facility free of charge. We want to give back to our community and educate people about the importance of protecting our wildlife.”
Lokotsch says the company is in the process of developing a long-term veld and game management plan in consultation with a wildlife veterinarian and environmental specialist.
“We want to understand the biodiversity and do the right thing ecologically in terms of the species that we introduce, the indigenous vegetation and the carrying capacity of the land.
“Currently, we have several free-ranging species such as various buck, giraffe, and zebra. There are no animals in cages and no dangerous game. All the big cats for which the park was previously known have been rehomed by the former owners.”
Development plans
With water for the animals being scarce, rainwater tanks have been installed and a borehole will be sunk to access a steady groundwater supply.
Lokotsch says the first phase of redevelopment will be completed within the next six to 12 months, beginning with high-security electrified fencing to keep out poachers, and keep animals and visitors safe.
The existing facilities, including the restaurant, log cabins, camp sites, ablution blocks and braai areas, will also be upgraded.
“Our vision is to have mountain biking and walking trails criss-crossing the property, so that it becomes a very special outdoor recreational centre that allows people to have close encounters with our incredible wildlife,” says Lokotsch.
“In the next two years, we aim to create 30 to 50 jobs in the local community, assisting with trail building and the removal of alien invasive species such as black wattle, which we will help them bag and sell as braai wood for additional income.”
Sustainable growth
He says the new investment aligns with the company’s existing sustainability efforts, such as the rooftop solar energy plant powering Jendamark’s Gqeberha manufacturing facility. In addition, aspects of Jendamark’s core business are having a positive environmental impact, such as the development of assembly solutions for electric vehicle power packs, as well as catalytic converters, which reduce harmful exhaust emissions.
“What we’ve realised as a tech business is that attracting and retaining specialised skills involves more than money,” adds Lokotsch.
“For the new generation of tech talent, shared values and wellness incentives are just as important as above-market salaries. So, we are constantly thinking of new and authentic ways to be a good corporate citizen and the employer of choice.”
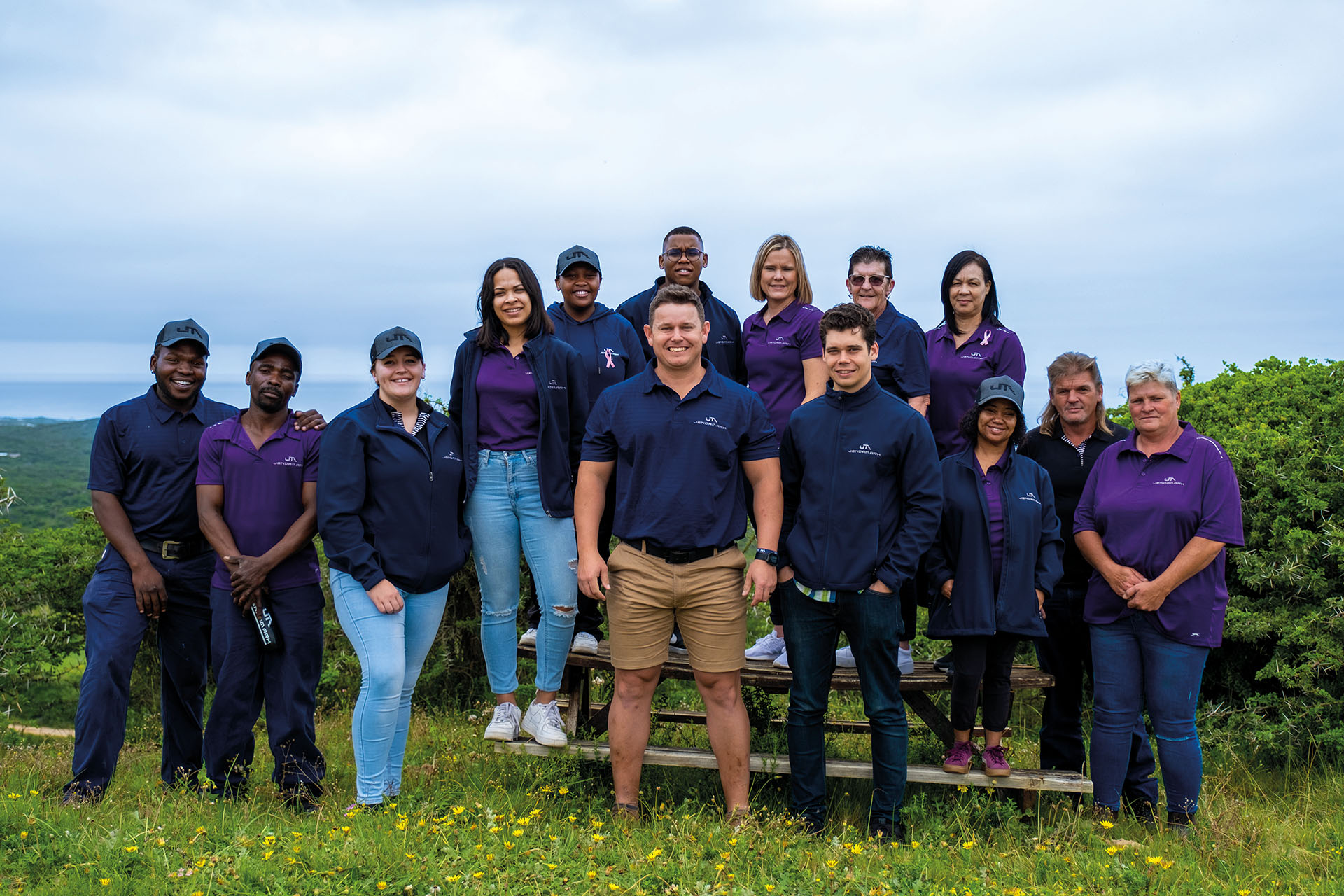
by NewsAdmin | Mar 7, 2023 | Jendamark News
Period poverty is the second biggest issue in Africa preventing educational equality for girls. Jendamark Automation has supported the start-up of Sisterhood SA Pty, a visionary health programme that is changing lives with a simple, sustainable sanitary kit.
While menstruation is a taboo topic in many communities, it has a very real impact on the lives of young women, who miss between 75 and 100 days of school every year because they either cannot afford or do not have access to sanitary products.
Enter Sisterhood SA Pty, which has designed a cost-effective sanitary kit that aims to educate and empower girls and keep them in school. The kit includes a washable, reusable sanitary pad and panties, available in pre-teen to adult sizes, plus low-cost cleaning products and educational brochures on reproductive health.
From start-up to success
The Gqeberha-based, women-owned company first engaged with Jendamark during the Covid-19 pandemic when likeminded local businesses started working together to set up supply chains and funding for struggling hospitals.
Seeing the opportunity to make a difference in a different direction, operations director Siegfried Lokotsch made start-up funding available, which allowed Sisterhood SA to develop test kits for a trial run at three schools in Gqeberha.
“The funding gave us the chance to complete our first manufacturing run with leading ISO9000 companies, following written approval from the South African Bureau of Standards to start production on the product and packaging.
“We were able to secure our patent and have a finished product to present to the international market,” says Sisterhood SA Pty director and founder Shaan Keegan.
“We are now in the process of finalising full production and, given the interest from the retail sector and corporate social investment programmes, especially in the USA, we will be starting in 2023 with 3000 units per day.
Partnering for growth
“We have established partnerships with our CSI partner New Africa Education Foundation, which can issue Section 18A tax certificates for corporate donors, and with Novartis Pharmaceuticals, which has a footprint into 47 countries in Africa. We are also endorsed by the United Nations Women’s Forum and Social Justice for Women in SA.”
Keegan says the product will first be distributed in South Africa, followed by Kenya and the USA, and then the rest of Africa, once cluster patents have been secured and they have entered into policing of patent agreements with these countries. She says recent discussions have taken place with leading international organisations such as the East African Health Platform, SOS Children’s Villages, and the Red Cross, as well as a chain of hospitals in India.
“Sisterhood SA Pty would not exist if it was not for Jendamark, so their constant support and contribution meant the world to us. The kit concept and the education programme have never been done before. We are now gaining global attention and, as per the latest interview at the Global Changemakers forum in the USA, we are being well received by Africa and the West.”
by NewsAdmin | Feb 21, 2023 | Jendamark News
Going to market in 2023 is the ODIN IOT platform, which gathers real-time performance data straight from customers’ machines to predict and avoid downtime. The technical product manager, Christine Chetty, explains what it’s all about.
Essentially, ODIN IOT is about unlocking everyday value from machine vibration data, says Chetty.
“Do you really know when and how all your critical assets are being utilised, or when the right time is to perform asset maintenance? ODIN IOT is designed to be a reliable source of asset utilisation data to help you make the right decisions whenever you need it.”
Chetty says the vibration data produces actionable insights in near real-time, so there is no need to pay an expensive specialist to come in at regular intervals and carry out an in-depth vibration analysis to extract meaningful information and predict problems.
“The subscription-based service gives you access to data that you wouldn’t normally have or possibly even understand. It makes it useful on a daily basis.”
For instance, she says, it enables the scheduling of just-in-time preventative maintenance, based on actual productivity, which reduces downtime and unnecessary spare part consumption. By predicting harmful trends in asset vibration, it can help customers uncover faults and use the ‘raise alert’ function to trigger action before any damage is done.
The IOT platform pairs with the on-device Raven sensor, which, Chetty explains, also allows customers to gain new insights into older machines.
“Mechanical machines can connect to the cloud without the infrastructure setup and expertise costs associated with most IOT system implementations.
“At Jendamark, we validate the insights produced on the grinder in our own machine shop. We can see that it’s consuming energy, even when it is idle or not producing parts. So then we have the data to show that it should be turned off to reduce non-productive expenditure.”
A new feature, which is a useful value-add, is that mobile app users can now input their own production data on the shop floor.
While this is not strictly an IoT core value, it is in line with ODIN Manufacturing’s vision to connect people, machines, and products, says Chetty.
“We are helping customers to digitise their processes. We’re talking about the kind of thing that would be noted manually on a whiteboard or a clipboard form daily. For example, if you scribble up your production targets on a whiteboard, you can now see the history of those targets over time.”
This, she explains, is ideal for small businesses that do not have a manufacturing execution system (MES) like ODIN Workstation collecting their production data.
“We are constantly trying to refine our understanding of our customers’ problems, and make a real, practical difference in their operations, which is what led us to completely re-architect our offering in 2021,” says Chetty.
“Often production problems aren’t complex. But why are there no existing digital solutions to these problems?”
This is what Chetty and the ODIN Manufacturing development team are working to answer.