by NewsAdmin | Jul 31, 2023 | Jendamark Junction
As part of a social investment partnership with Rotary International, Jendamark India and suppliers recently sponsored 38 Odin Education tablets to 8th grade students at the SAMPARC Gramin Vidya Vikas Kendra School in the village of Bhambarde in Mulshi Taluka.
SAMPARC, which stands for Social Action for Manpower Creation, is the brainchild of Shri Amitkumar Banerjee, who started this organisation of hope in 1990 for children of sex workers as well as orphans and destitute children. It works in Jendamark India’s home state of Maharashtra and in Rajasthan, West Bengal and Uttar Pradesh, offering services ranging from children’s homes to community education support programmes, industrial and vocational training centres, and schools.
SAMPARC started its second centre in Bhambarde to give poor children from nearby rural villages a chance to attend school. Recently named the best school in Mulshi Taluka, the award-winning Bhambarde Gramin Vidya Vikas Kendra now has a hostel and facilities for 281 students from the 5th to 12th grade and offers the finest computer class in the district.
Rotary Club of Pune Wisdom identified the school as the right fit for this ed-tech sponsorship. The 8th grade students were introduced to the Odin Education ecosystem and received their ed-tech tablets, which were pre-loaded with their syllabus content and related educational resources and learning platforms. As individual students engage with the device, they will also be served with content about specific subjects and activities they are interested in that don’t form part of their curriculum.
Special thanks to Jendamark India’s partners in this project: Sandesh Cargo Movers, S.P. Engineering, Sai Industries, Shree Ganesh Packers, Santech Systems, Shruti Transport, Swiftin Corporation LLP, Access Industrial Sol, Sigma Tools & Machine Solutions, Swara Industries, and S.B. Rubber & Engineering Industry.
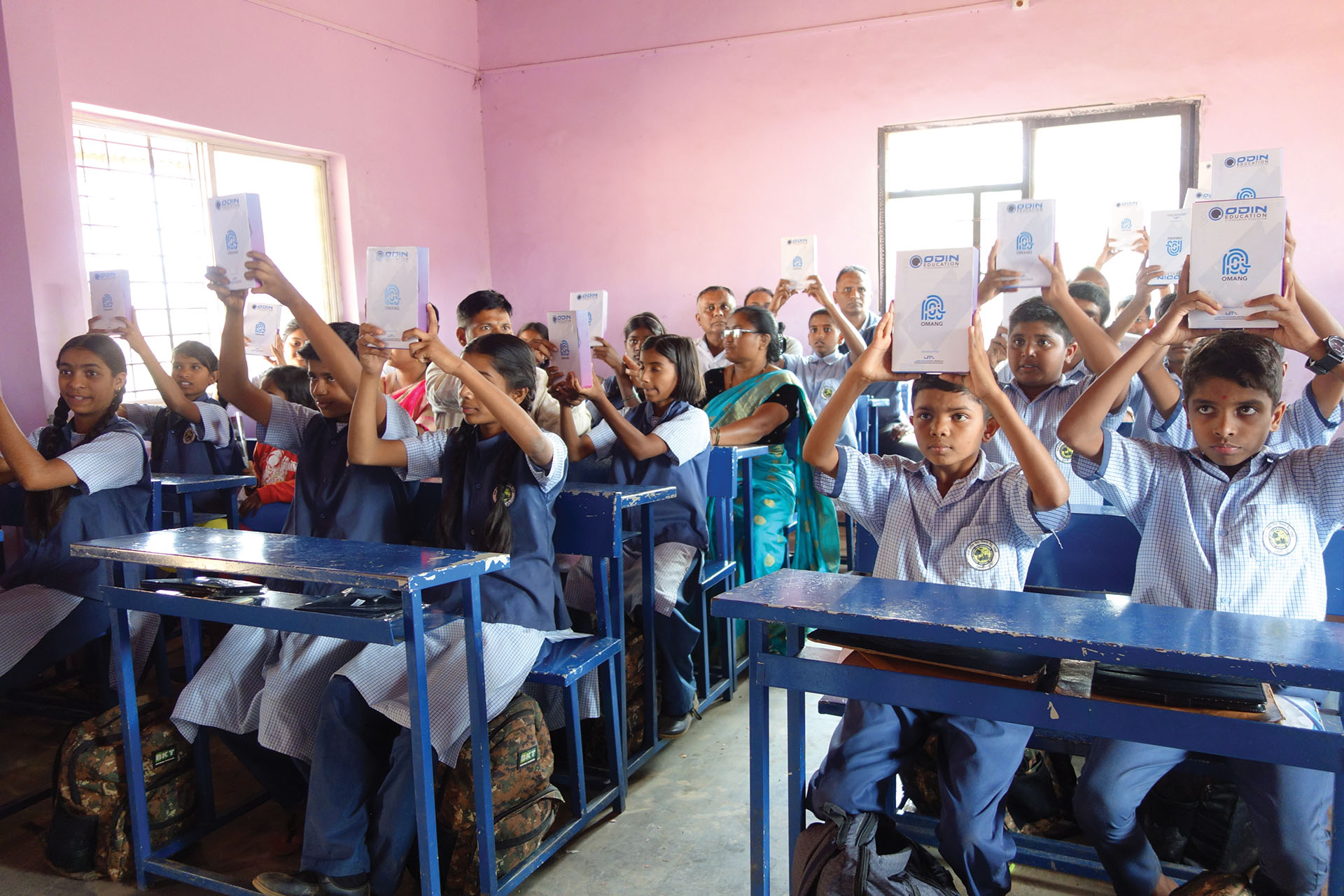
by NewsAdmin | Jul 28, 2023 | Jendamark Junction
Educational technology, or ed-tech, is not a new concept, but the radical infrastructural approach that ODIN Education has developed is successfully bridging the digital divide in classrooms across India and South Africa.
Right now, there is a huge opportunity to transform education in developing countries, the head of ODIN Education, Ajit Gopalakrishnan, believes.
“The need for change in education isn’t new. Ed-tech itself isn’t new – some companies have been doing it for close to 20 years,” says Gopalakrishnan.
“But there are significant infrastructural challenges in developing countries that widen the digital divide. At ODIN Education, we believe we can fill in the gaps in accessibility to education and technology. Our aim is to be a complete infrastructure solution, and to develop a way for ed-tech to be implemented at scale.”
Full stack solution
Gopalakrishnan describes ODIN Education as a “full stack” solution.
“We put the entire infrastructure in place – everything from hardware to software, and we also provide support for what we call warmware – the students and teachers themselves.”
ODIN Education deploys ed-tech devices, personalised for every learner and pre-loaded with educational resources, which are all connected to the cloud server.
“It’s a safe, managed solution. Our system is closed, and the children can access only what we open to them,” he says, adding that analytics currently show substantial engagement – an average of 51 minutes per learner per day.
Where there are larger constraints such as poor connectivity in far-flung rural areas, the system provides a mix of online and offline resources.
Holistic education
“We don’t believe that fully online learning and teaching is the solution, but at the same time, traditional ways of teaching are outdated. So, our approach is a hybrid one, deploying tech into schools to sustainably augment the learning process.”
Essentially, Gopalakrishnan says, there are two problems to solve: access to resources and the education system itself.
“We cannot treat every child the same. We need a dynamic, personalised curriculum that understands the child and the environment they are in.
“I don’t believe we have a shortage of talent or passion. What we are creating is the infrastructure to find the talent and nurture it.
“The integration of AI helps us figure out what a particular child is good at and interested in, and then to connect that child to the resources they need to develop their talent. We can be pioneers in a new way of educating.”
ODIN Education is currently being rolled out with the support of private companies who have the vision to invest responsibly and sustainably in the future.
by NewsAdmin | Jul 27, 2023 | Jendamark Junction
The Government of India has introduced a new set of rules under the AIS 156 banner, designed to regulate electric vehicle (EV) assembly, given the complexities and incomplete technical expertise of this burgeoning industry.
Electric vehicles have been holding their own since entering the global market, as they offer significantly lower running costs and less environmental pollution than internal combustion engine (ICE) vehicles. An EV consists of many electronic parts and a large cluster of wires connecting them to the battery and motor, which contributes more than 50% of the vehicle’s total weight and price.
Because battery packs tend to have more safety and operational issues than other components, the new AIS 156 regulations call for a data-driven assembly process and more control over the manufacturing of EVs.
Standard requirements
The AIS 156 standards require manufacturers to store cell grade and quality data, like Open Circuit Voltage (OCV) and Internal Resistance (IR), as well as the cell manufacturer data, against the serial number for each cell prior to assembly.
After assembly, the total battery pack OCV and IR must also be recorded, as it is mandatory to put the same grade of cells in a single battery pack. This is essential for maintaining the quality and safety of the EV.
According to Jendamark India director Himansha Jadhav, Jendamark has put automation solutions in place to help manufacturers measure these values and place cells as per their grading.
“ODIN Workstation records the data with which it controls the process to ensure that the graded assembly of battery packs is followed.”
“Another parameter is Ingress Protection (IP X7) standards for water and dust-resistant packaging of battery packs. Manufacturers will have to perform leak testing for which we provide automation, process security, and data capturing of leak and pressure values,” explains Jadhav.
In addition, AIS 156 also lists testing requirements for battery management systems, thermal management and charge-discharge of battery packs.
“For this, we have successfully integrated with the testing machines, and store data to decide whether the battery pack is built as per requirements. All this data can be seen against the serial number of each battery pack.”
Supporting complex assembly
“In India, up to 75% of workers are contract based, which results in an untrained and inexperienced workforce. Add to that the revolutionary and complicated nature of the EV product, and there is a clear need for extensive operator training and guidance,” explains Jadhav.
A process security system that will ensure product quality and protect the operator from harm is essential, he adds.
“In this era of Industry 4.0, manufacturers need data traceability, providing analytics for each process, and to be able to manage different variants on a production line.
“Jendamark’s homegrown software solution includes Odin Workstation, which handles all these complexities and ensures right-time assembly every time.”
Step-by-step operator guidance on an interactive touch screen allows workers to easily follow the set process for assembling each type of battery or variant, while enabling companies to spend less time on training.
“We’ve seen companies putting a lot of time, money and sweat into developing products and building prototypes necessary for the certification to launch the product, but that doesn’t always translate into the production being done with the same amount of care, comfort and expertise,” cautions Jadhav.
“We know there is a need to meet production volumes to fulfil market demand, but an incorrectly assembled product can be disastrous for any company, leading to product recall campaigns.”
Because ODIN Workstation is integrated with on-field devices like cameras, tightening tools, sensors and leak test machines, it will not allow the operator to skips steps. This ensures that products are correctly manufactured every time.
Looking ahead
Jadhav expects data-driven process control to become a required norm in the near future.
“Manufacturers are already upgrading the manufacturing process to include a mix of automation and process security for their assembly line. This ensures optimum use of investments and 100% right production output.
“Jendamark, having developed and deployed such solutions, is already ahead and ready to deploy more such solutions. We have also dedicated substantial resources and already offer our customers new technology solutions such as AI-based vision systems, collaborative robots, and IOT sensors in proof-of-concept stage.”
Interested in our process security solutions? For more details, contact shashikant@jendamark.in
Complex EV assembly Solutions
Jendamark provides customised solutions, with built-in process security, for these EV assembly challenges:
- Potting and dispensing of phase-changing material in battery packs
- Cell sorting, grading and cell formation
- Laser welding of busbars to cell terminals
- Motor magnet dispensing and motor winding
- Handling electronic components with minimum manual intervention
- Thermal pad compression and strapping of battery packs
- E-transmission with gauging and shim selections or integrated drivetrains
- Torquing, traceability, testing and integration of all systems in one
by NewsAdmin | Jul 26, 2023 | Jendamark Junction
The introduction of ODIN Workstation on a new differential assembly line for our customer, ZF, at their plant in Gainesville, USA, has made a big difference to the operators on the shop floor.
According to ZF’s senior production support specialist, David Pirkle, the human-centric approach is not only helping operators to do their jobs better but is also helping the plant to achieve its overall key performance indicators.
“We concentrate on four Lean manufacturing principles: We want a safe plant that doesn’t put the customer at risk, that makes good quality products, and we want to be able to do this at a good cost, and in time. If we achieve those four KPIs at a high level, then we’ll have customer satisfaction.”
Pirkle says taking a human-centric approach by first supporting operators is essential to achieving this success.
“If we continue to make their job easier, we’ll get the KPIs we want.”
Paperless work instructions
While some were initially resistant to the switch from paper-based work instructions to a step-by-step digital process, Pirkle says even the longest serving operators have seen the difference it has made, since they no longer have to memorise the steps.
“One operator, he’s a little old-school, came back and said this was actually easier than paper. So I was happy to hear that because I really value him – he’s been with ZF for 35 years.”
Pirkle said ODIN Workstation provided practical support for operators, helping them follow a set sequence to build quality products in a safe way, within cycle times.
“ODIN is right in front of them, showing them what to do. The operators can basically build and look at the same time.
“It also allows you to train less, because the work instructions are in front of you, they’re easy to read and simple to understand. If something doesn’t go right, ODIN tells you what you’ve missed. It won’t allow you to move to the next step unless you do the previous one.”
Aside from work instructions, ODIN Workstation secures the process via validation of parts and sub components. Traceability of every step allows visibility into process, product and machine trends generated from automated, semi-automated and manual operations.
TPM and 5S checks
ZF also worked with Jendamark to develop a new system within ODIN for ensuring that operators complete their required Total Productive Management (TPM) and 5S System checks, to ensure that their space is clean and organised so work can be performed efficiently, effectively and safely.
“The operator comes in in the morning, and they’ll do their quick 5S checks. Then they click ‘Yes’ to accept responsibility for the state of their work area and start their shift. This drives accountability, and we’ve seen a really good response,” explains Pirkle.
“The supervisor loves it because he doesn’t have to walk around the line and he doesn’t have to check the boards; the information comes to him. Because a lot of the data is in ODIN, which can produce graphs and charts for reporting, supervisors can actually supervise again and not be so tied down with admin.”
Given the benefits that the Gainesville plant has seen, ODIN Workstation will also be adopted at its sister facility in Marysville.

GLOBAL TEAMWORK
This assembly line was an example of Jendamark’s global teamwork – designed, built and installed by our South African team, with the high quantity workpiece carrier units manufactured in India.
It was also installed in record time – 7.5 weeks from the time the first box arrived until the last button was pushed and final sign-off achieved.
Project manager David Boshoff says the recipe for success was testing and more testing. “Through proper strain testing at our home premises, we could de-bug the line and avoid a costly, extended installation.
“This was our first time using VMT to scan and evaluate the sealant bead. Getting the spintop working on site brought many unknowns and was challenging, but the team dug in and resolved all issues.”
Boshoff says pandemic-related visa restrictions meant that all installation team members had to climb in to make it happen. “We had controls guys wiring panels, mechanical building parts and electrical helping with line layouts.”
A further headache was the delayed arrival of a third-party supplier’s robots.
“It was a challenge placing the conveyor in the exact location, within 10mm, to ensure that they could reach pick-up and drop-off. We had to measure and re-measure many times before placing the conveyor and then all the facilities. Moving the entire line again was out the question.”

by NewsAdmin | Jul 25, 2023 | Jendamark Junction
Jendamark’s manufacturing technologies have been independently recognised for a second consecutive year by the prestigious Africa Tech Week Awards in Cape Town.
At the ceremony in May, Jendamark won the Technology Innovation of the Year category for our ODIN Manufacturing software, making it two in a row after being named Technology Company of the Year for 2022.
Innovations director Yanesh Naidoo says the award, judged by an independent panel, serves as a confirmation that the manufacturing technology developed by Jendamark is meeting a real need for small to medium enterprises.
“For us, it’s not about developing technology for technology’s sake, but about understanding the customer’s challenges, and creating digital solutions to solve those challenges.
“Last year, the award was about our company; this time it’s for our products. So, it’s a massive win for us,” says Naidoo.
For developing countries such as South Africa and India to prosper, he says, there is a need to focus on building a strong manufacturing-based economy.
“That’s why we developed ODIN Manufacturing – to help digitise and improve production efficiencies, and create opportunities for the massive human capital that we have.
“Our solutions take a human-centric approach to Industry 4.0, meaning they don’t take people off production lines but rather use tech to support people to do their jobs more accurately and efficiently.”
Jendamark’s ODIN Education division, which creates the tech infrastructure to bridge the digital divide in underprivileged schools, was also named a finalist in the ed-tech category.
“Although they may seem unconnected, we created ODIN Education to help transform the education sector, so that the next generation can be equipped and ready to take on this manufacturing challenge amid the rapidly accelerating pace of Industry 4.0 technologies,” says Naidoo.